Fully automated guided vehicles
Time pressure, efficiency requirements and the demand for top performance characterize your industry. Staff shortages, rising costs and a lack of automation expertise make success difficult. This is where automated guided vehicles (AGVs) offer a solution for process optimization.
AGV Automated guided vehicles
An automated guided vehicle (AGV) is an automated conveyor whose main task is to transport materials for production and logistics processes. Automated guided vehicles move goods of different sizes, masses and shapes along a network of routes, from simple standardized transport boxes and pallets to complex components and entire workstations.
Automated guided vehicles are often used as a coordinated network, forming an automated guided vehicle system (AGV). In an automated guided vehicle system, several AGVs are networked together and work together to efficiently organize and control material movements within a specific area, such as a factory or warehouse. Sensors and navigation systems enable the AGVs to avoid obstacles and move smoothly in the shared traffic area. This allows them to continuously transport material, optimize workflows and automate the overall flow in logistics or production.
Roadmap for the successful implementation of an AGV project
Advantages of automated guided vehicles - AGVs
Costs of AGV
By eliminating drivers and reducing errors and accidents, operating costs can be lowered. With conventional logistics vehicles, 80% of costs are accounted for by personnel costs alone.
Reliability of AGV
Self-driving vehicles can be used around the clock. Material flows are optimized through automation, which significantly increases handling capacity.
AGV safety
AGVs reduce the risk of accidents and injuries by using automated safety protocols. As a result, the costs of damage are minimized. The AGV expert opinion provides information on the safety of a system.
FAQ - Frequently asked questions about automated guided vehicles (AGVs)
What is an automated guided vehicle (AGV)?
An automated guided vehicle (AGV) is an automated means of transportation that is mainly used for transporting materials in production and logistics processes. Automated guided vehicles transport goods of different sizes, weights and shapes over a defined network of routes, from standardized transport boxes and pallets to complex components and complete workstations.
What is the difference between autonomous mobile robots (AMR), automated guided vehicles (AGV) and automated guided vehicles (AGV)?
Automated guided vehicles (AGVs) consist of one or more automated guided vehicles (AGVs) and operate on fixed routes with centralized control and are suitable for predefined tasks in stable environments, while autonomous mobile robots (AMRs) navigate flexibly and intelligently in dynamic environments by using sensor technology and artificial intelligence. AGVs offer less flexibility, while AMRs can automatically adapt to changes and work efficiently in real time.
What different automated guided vehicles are there?
Different concepts of automated guided vehicles have been developed for the various transportation requirements in logistics and production. The following transport vehicles are used most frequently: fork-lift AGVs, piggyback AGVs, tractor AGVs, underride AGVs, assembly AGVs, heavy-duty AGVs, mini AGVs, outdoor AGVs and special AGVs.
What advantages do automated guided vehicles offer?
The systems offer high scalability by expanding the number of automated guided vehicles (AGVs) and transfer stations as well as the option of implementing layout changes. They adapt well to fluctuations in dynamic material flows and enable the safe and reliable transportation of almost any conveyed goods by adapting the load handling device.
Are automated guided vehicles safe?
Automated guided vehicles (AGVs) are safe because they are equipped with advanced sensors, real-time monitoring, emergency shutdowns and intelligent route planning to avoid collisions and ensure consistent performance.
What applications are automated guided vehicles suitable for?
Automated guided vehicles (AGVs) are ideal for use in warehousing, logistics, production, hospitals, airports, retail and various industries. In principle, they can be used anywhere where goods need to be transported regularly.
Which automated guided vehicle system is best suited to my application?
We can discuss your requirements in a personal consultation and in the AGV basic check we will show you whether the system is technically feasible and economically viable. You can also take a look at our white papers, which provide you with valuable knowledge about AGV projects.
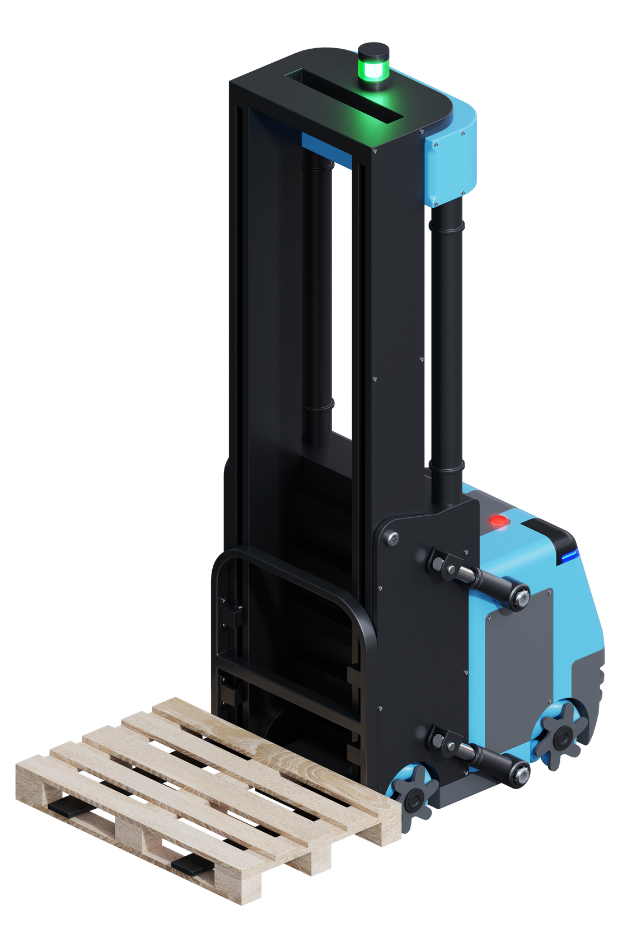
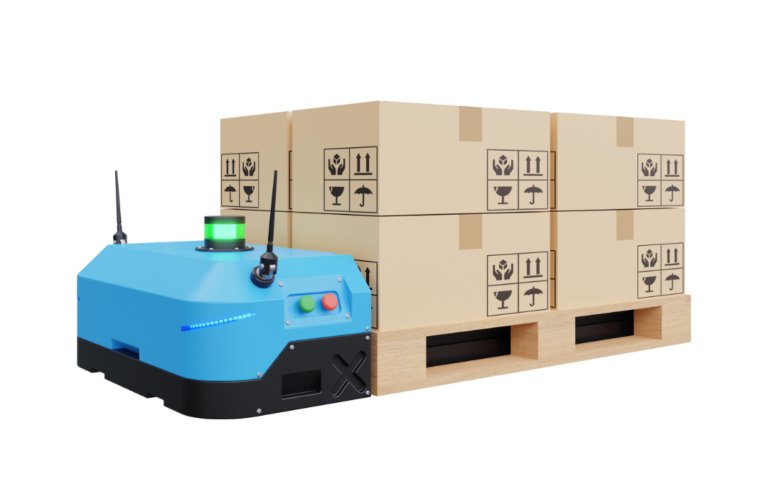
Components of automated guided vehicle systems
Automated guided vehicle systems consist of one or more automated guided vehicles (AGVs), a control system, a location determination system, a data transmission system and the infrastructure with peripheral equipment.
An automated guided vehicle (AGV) essentially consists of a chassis, a computer, one or more drive(s), the power supply, a load handling module, a communication module, a safety component and a user interface.
If you would like to learn more about automated guided vehicle systems, we recommend our AGV basic training course or our free white papers.
Navigation concepts for automated guided vehicles (AGVs)
Choosing the right navigation method is a decisive factor for the success of your automated guided vehicle system. ProLog Automation has the necessary expert knowledge to ensure that the navigation is perfectly tailored to your requirements. Below is an overview of the most common types of navigation:
Physical lane-based navigation
These cost-effective solutions use guide wires, magnetic tapes or colored lines that the vehicles follow on a fixed lane. The disadvantage of this installation is its limited flexibility and susceptibility to damage.Virtual track-based navigation
Technologies such as magnetic point/grid navigation or laser triangulation combine high precision with flexibility. Instead of physical tracks, these systems use digital maps or magnetic grids, which makes them more versatile.Free (autonomous) navigation
With contour navigation (SLAM), vehicles adapt independently to their surroundings. This method requires no additional infrastructure, but reacts more sensitively to changes in the environment.
With ProLog Automation you will find the ideal navigation solution for your individual requirements.
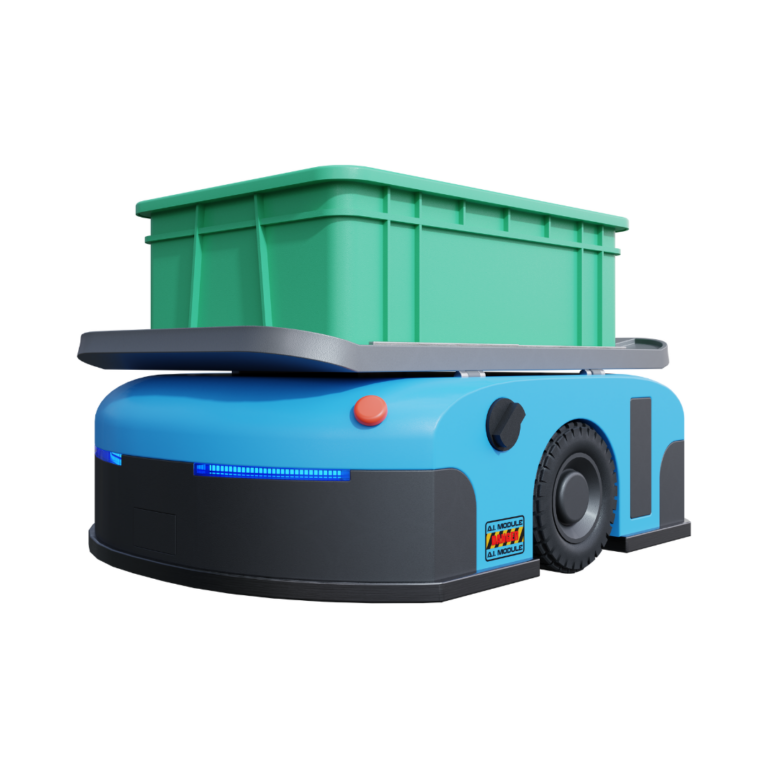
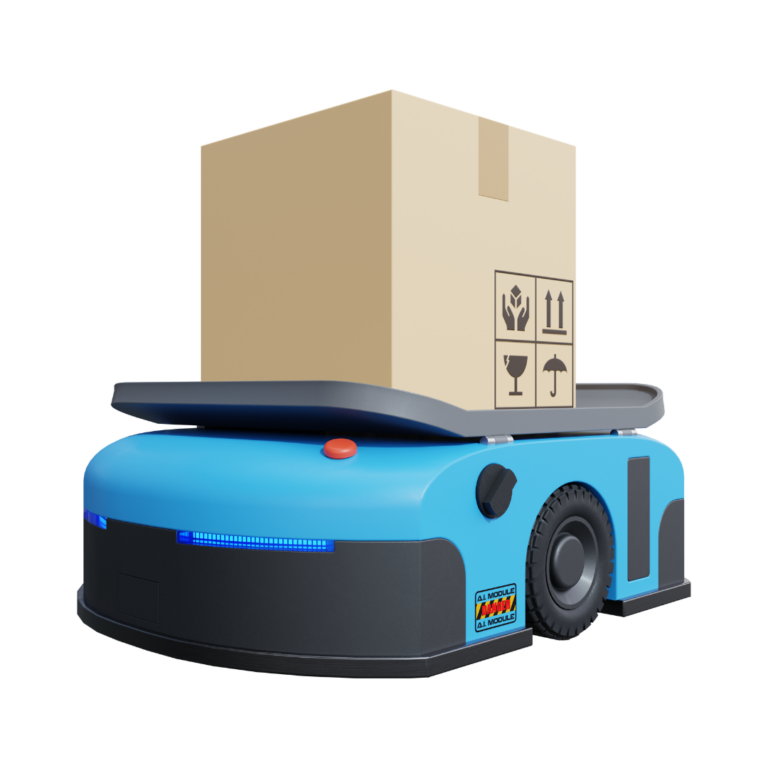
Safety concepts for automated guided vehicles (AGVs)
Safety has top priority! Automated guided vehicles are equipped with state-of-the-art safety solutions to ensure safe operation and the protection of people and equipment.
Active safety systems
- Personal protection scanner: Dynamic adaptation of the safety fields to the speed of the AGV. Persons in the warning area automatically cause the speed to be reduced or the vehicle to stop.
- Ultrasonic sensors: Reliable obstacle detection, insensitive to dust, moisture and ambient light.
- 3D cameras: Precise detection of obstacles such as overhanging loads or forks of other vehicles.
- Visual and audible warning signals: Directional lights, indicators and audible warning signals ensure maximum visibility and safety, especially in areas with high traffic volumes.
Passive safety systems
- Bumpers: Mechanical bumpers that stop the AGV immediately on contact.
- Emergency stop button: Manual emergency stop functions that enable a quick response in dangerous situations.
Our expertise enables us to provide you with comprehensive advice on the safety of automated guided vehicles – so that your system is optimally protected.
Difference between load-pulling and load-carrying automated guided vehicles (AGVs)
Automated guided vehicles (AGVs) are a central component of modern intralogistics systems. Depending on the intended use, a basic distinction is made between load-carrying and load-pulling AGVs.
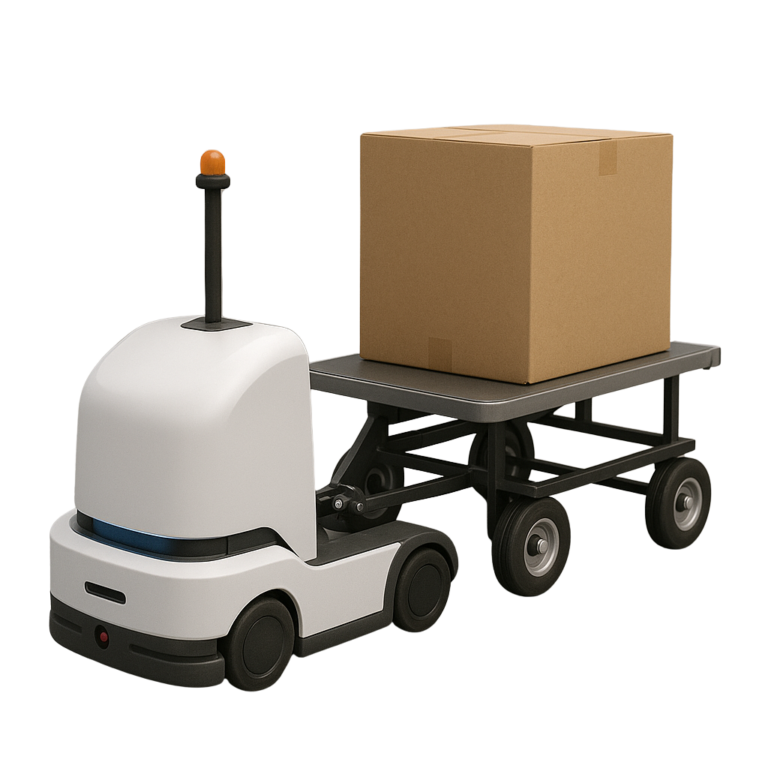
Load-pulling AGVs – pulling trailers
Load-pulling AGVs are designed to pull trailers or tugger trains carrying the transported goods. They act as tractor units and are often used as part of lean or just-in-time logistics processes.
Typical configurations are
- Tugger trains with several trailers
- Electric tug with coupling system
Area of application:
Particularly suitable for sequenced delivery in assembly, e.g. in the automotive industry.
Advantages:
- High transport capacity
- Bundling several transports
- Ideal for cycle and line supply
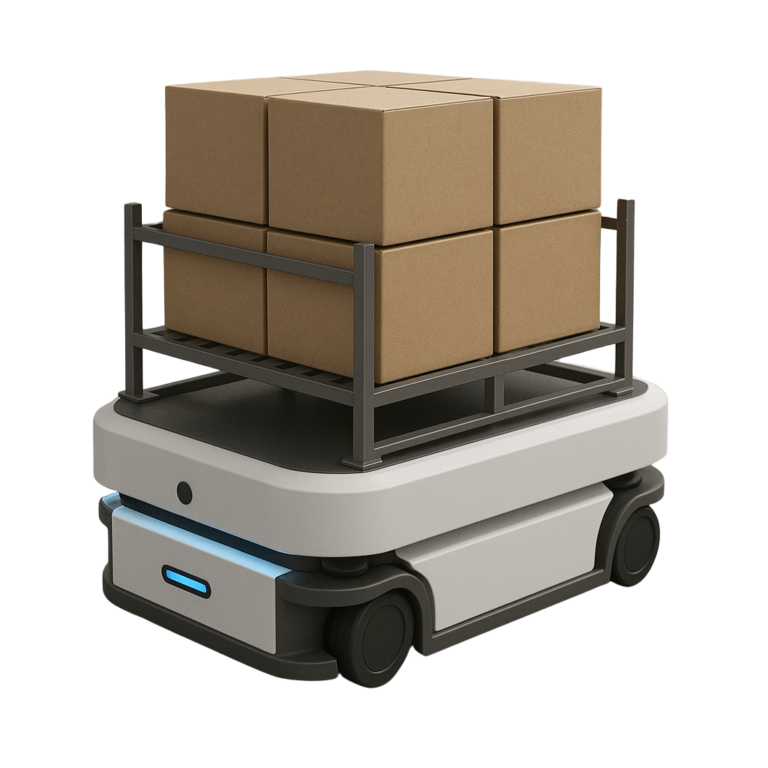
Load-carrying AGVs – transportation on the loading area
Load-carrying AGVs transport their freight directly on the vehicle. The load is carried on an integrated loading surface, a lift table or via special attachments such as conveyor belts, rollers or forks.
Typical examples are
- Platform vehicles
- Fork AGVs (e.g. driverless forklift trucks)
- Conveyor technology-FTF with roller conveyor or belt
Area of application:
Ideal for the in-house transportation of small load carriers, pallets or workpiece carriers over short to medium distances.
Advantages:
- Precise transportation of individual goods
- Integration of conveyor technology possible
- Flexible for various loading aids
AUTOMATED GUIDED VEHICLES
The benefits of automated guided vehicles at a glance:
Flexible
Tailored to individual requirements: Automated guided vehicles can be used flexibly and can be adapted to changes.
Load reduction
As automated guided vehicles take on heavy and repetitive tasks, they reduce the physical strain and risk of injury for human workers.
Increased efficiency in material flow
An automated vehicle works reliably 24/7 – without any breaks. This optimizes throughput times, minimizes downtime and significantly increases productivity.
Automated guided vehicle system in high-bay warehouse
Automated guided vehicles act as an intelligent automated guided vehicle system in high-bay warehouses, automatically and precisely storing and retrieving goods.
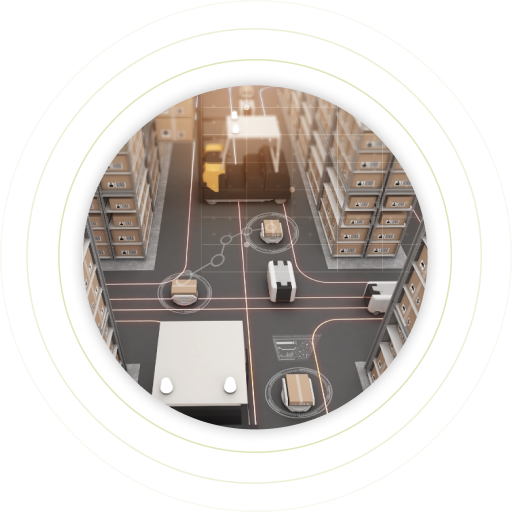
Long-term cost reduction
Long-term reduction of operating costs, personnel costs and error rates ensures a rapid return on investment (ROI) of the acquisition costs.
Security
Automated guided vehicles are equipped with sensors and advanced safety systems that prevent accidents and collisions.
Traceability and transparency
Automated guided vehicles are often integrated into digital systems that enable real-time monitoring and tracking of materials and products.
Scalability
An automated guided vehicle can be expanded on a modular basis. New vehicles can be easily integrated into existing systems to flexibly meet increasing requirements.
Experts Team
Satisfied customers
Projects
Arrange your AGV consultation
Our dedicated team of experts will be happy to help you further Your request is our mission to provide you with excellent service.
We look forward to your message.
Make an appointment directly
Our AGV and AMR expert Felix Imhof is available to answer any questions you may have about your AGV project.